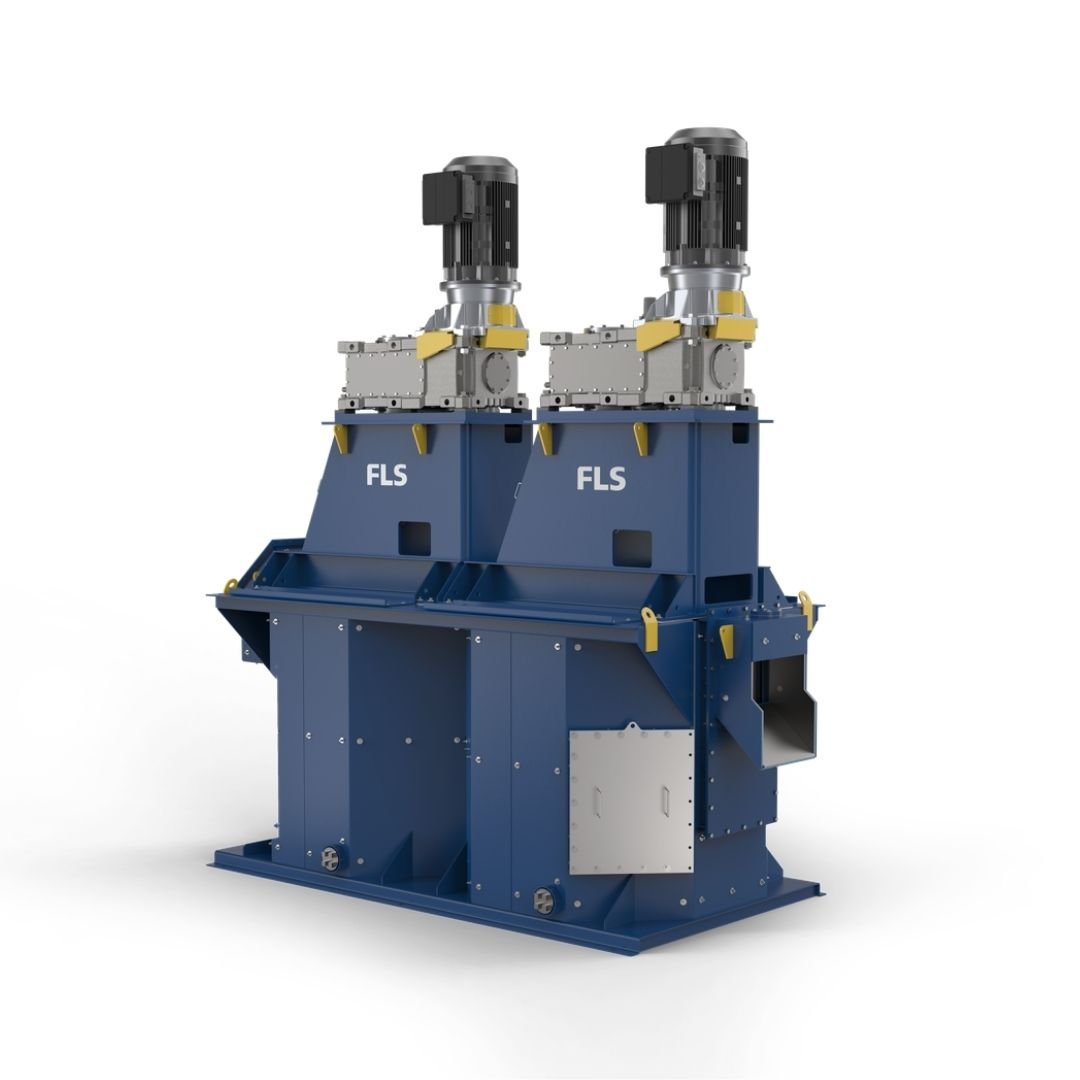
Explore our flotation equipment
Total lifecycle support of your froth flotation equipment
We offer the complete flotation package, from superior equipment and complete flowsheets to equipment surveys and sample testing. Every project is custom engineered to fit your application, regardless of the size, and supported at all stages from design, installation, and commissioning. Our aftermarket services include OEM-standard spare and wear parts that minimise downtime while optimising operation; global technical support services for maintenance, performance analysis, and optimisation; and accessible upgrade packages that ensure your flotation cell stays at the cutting-edge of performance.