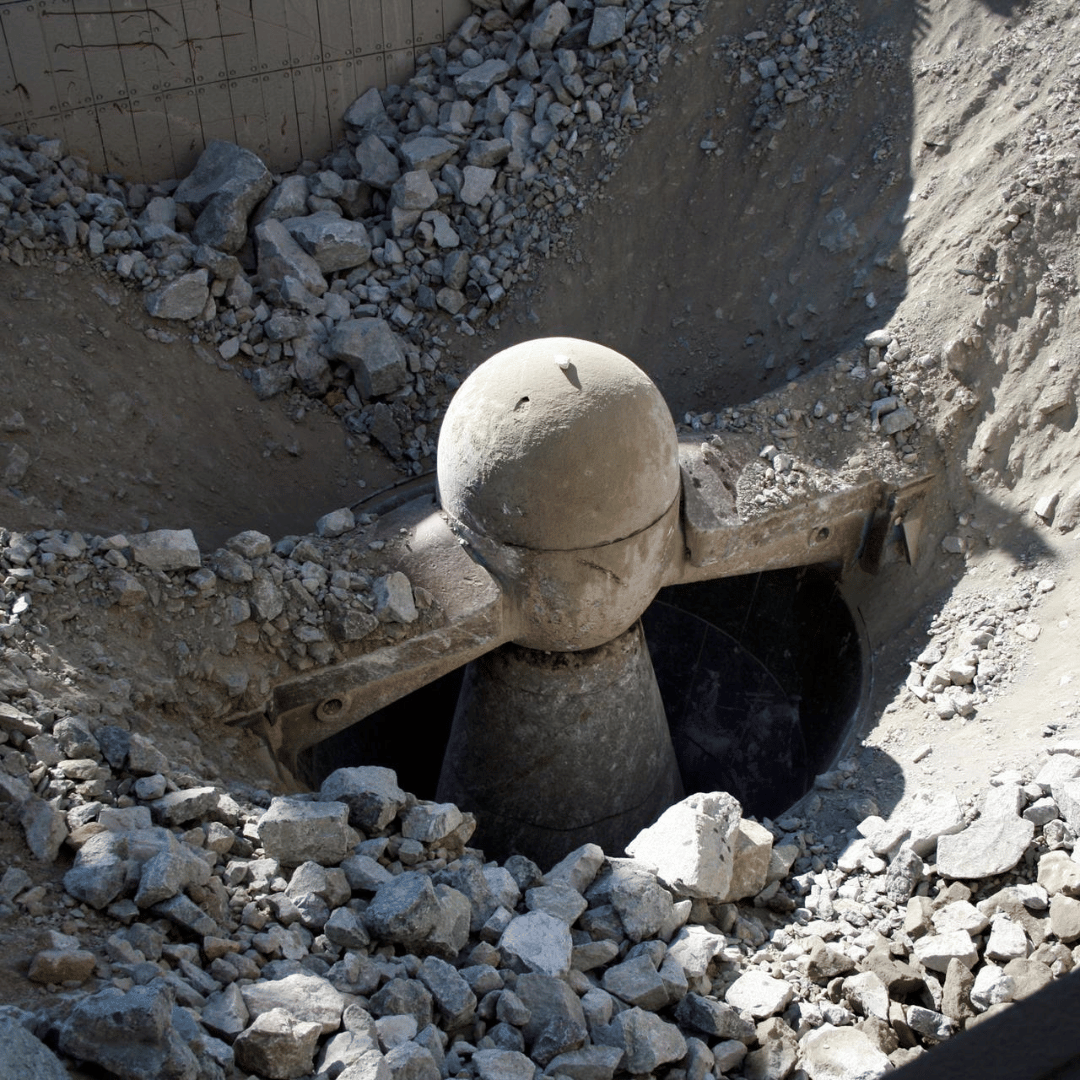
A track record of innovation and optimisation
Up to 15%
lower energy consumption with our HGPR Pro grinding solution.
High pressure grinding rolls
Up to 10x
higher throughput with the REFLUX™ Flotation Cell (RFC™).
REFLUX flotation cell
Up to 30%
lower pump power consumption.
Slurry pumping
Up to 95%
of your water can be reused with EcoTails™ filtered tailings.
Filtration and dewatering
20-85%
energy and tension reduction with the Rail-Running Conveyor.
Conveyors
Our greenfield flowsheets

Gold flowsheet
As ore grades decline and mine lives shorten, our flowsheets for gold and other precious metals keep CAPEX down and ensure economic recovery rates of even low-grade refractory ores.

Copper flowsheet
Copper mines are digging deeper and into increasingly harder rock. Our copper flowsheets optimise each step of the process, from comminution to filtration, to deliver efficient, low-cost productivity.

Iron flowsheet
Iron ore is all about volume. Our complete iron ore flowsheets deliver the largest possible throughput using reliable and robust equipment able to withstand even very high tonnages with minimal downtime.

Lithium flowsheet
Whether you own a lithium brine or hard-rock deposit, our CAPEX-efficient lithium flowsheets offer fast setup and cost-effective extraction of this critical metal while reducing environmental impacts.
Want to talk? Reach out to our experts
Next level grinding efficiency starts here
Looking to raise throughput, reduce operating costs, and improve energy efficiency? Our latest-generation HPGR Pro grinding solution delivers all this and more.